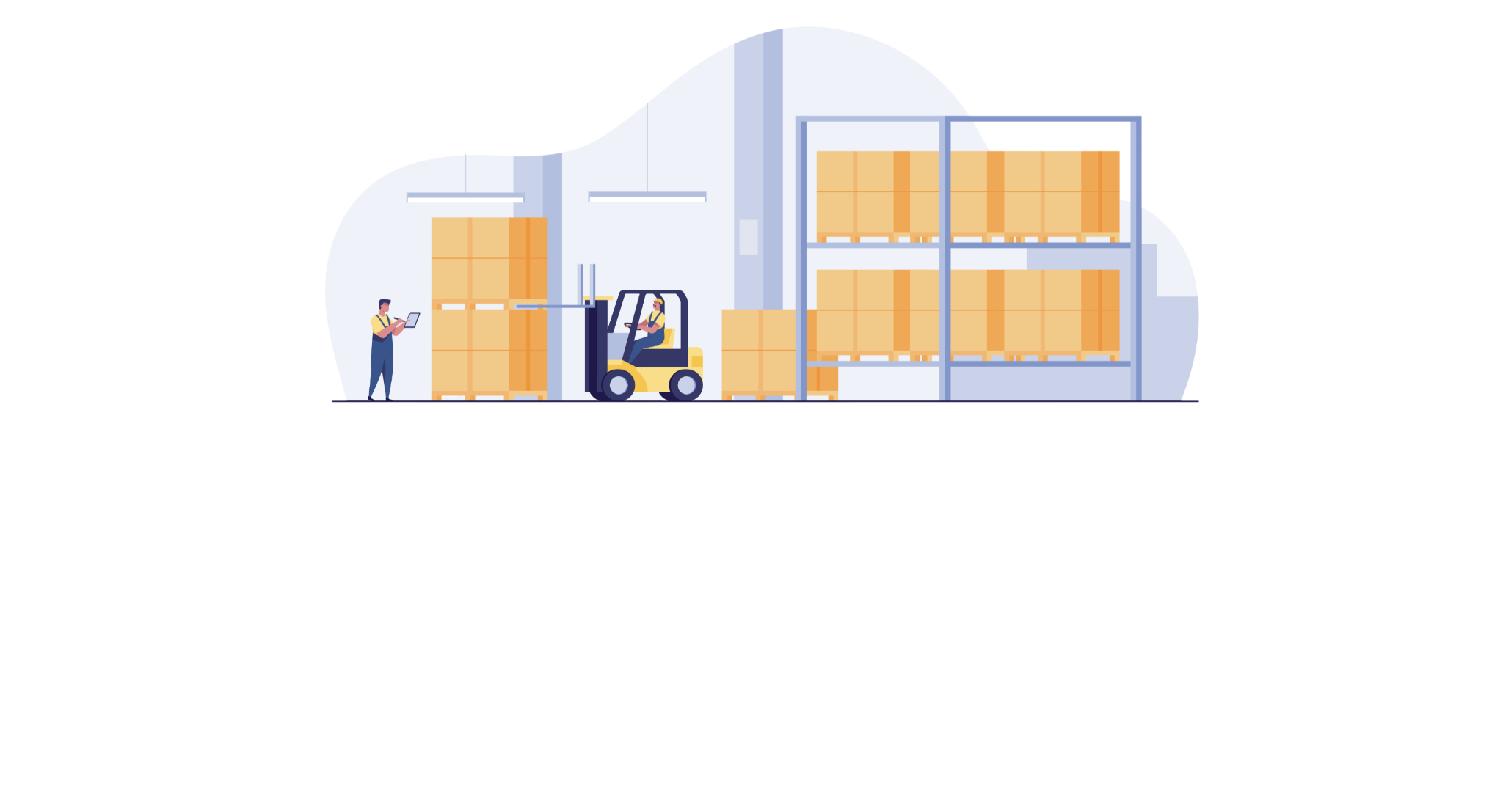
Warehouse service
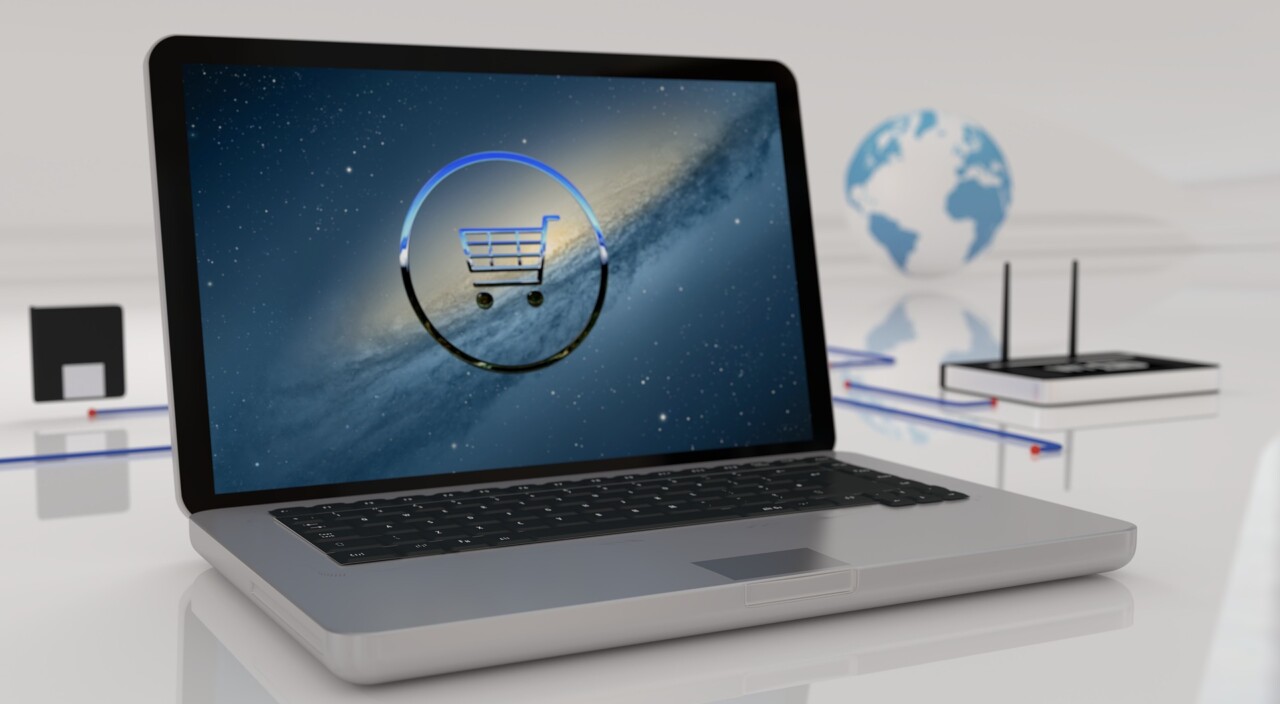
What does the receipt of goods into the warehouse look like?
1. Plan the goods receipt and unloading activities.
Planning the receipt of goods ensures the smooth operation of the warehouse. It involves proper communication between the warehouse and the goods carriers and suppliers. We ensure that those responsible for receiving the goods have all the necessary information and documents before the carrier arrives.
2. We verify the goods, documentation, and quality control.
The Warehouse Coordinator / Warehouseman, searches in the computer system (WMS) for the order and checks it against the delivery document. Under a given order, he registers the delivery in the WMS by entering the data from the delivery specification, i.e. the name of the supplier, specification number, date of delivery. Checks that the delivery is accompanied by a quality certificate or a note in the delivery note that the delivery complies with the FCA requirements and/or the manufacturer’s requirements accepted by the FCA.
3 We label, consolidate the goods, and distribute them in the warehouse.
Once the receipt of the goods has been approved, the Warehouseman/Warehouse Coordinator prints a label with the name and quantity of the goods, which is affixed to each pallet/package. Before unloading the goods, if any discrepancies are found, the Warehouse Manager informs the Warehouse Leader/Coordinator/Warehouse Manager, who decides on the further course of action.
Goods that have received a negative assessment are subject to withdrawal from the warehouse or re-sorting and re-packing, by arrangement with the Logistics and Procurement Department
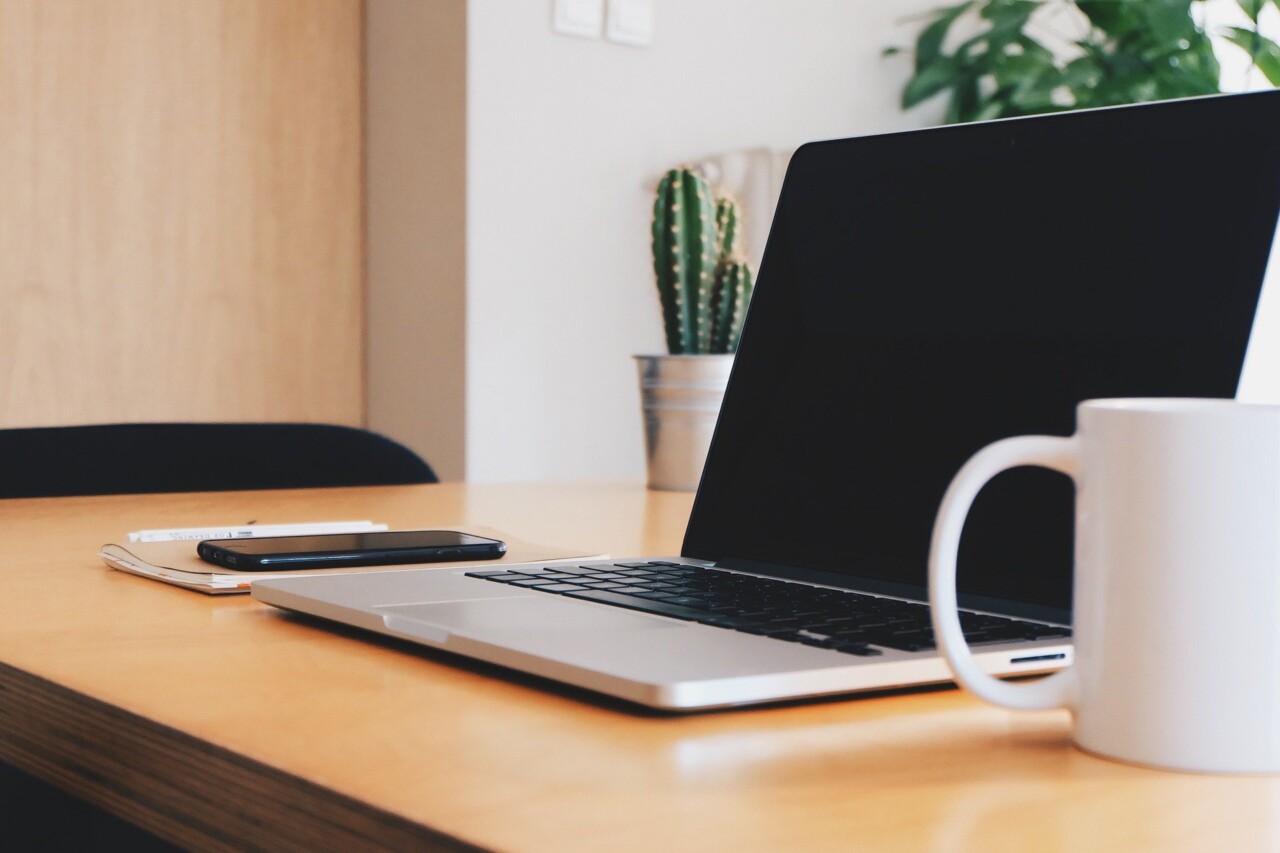
What programs do we use?
- Qguar WMS Pro (Warehouse Management System Pro) from Quantum – the warehouse management system we use at FCA. The software supports all warehouse processes, from the receipt of goods, through storage, picking to the issue of goods to the customer.
Qguar WMS Pro can be integrated with any software, i.e. ERP systems (SAP, Microsoft, Oracle, Comarch, Asseco and others). The software can cooperate, among others, with the following management systems: transport (TMS), yard (YMS) or production (MES/APS).
What are the benefits of using Qguar WMS Pro?
– faster receipt and release of goods,
– increased speed and correctness of picking;
– ordering and optimisation of warehouse processes;
– support for rule compliance (FIFO, FEFO)
– Transparent company logistics;
For more information, visit the manufacturer’s website. See more!
- enova365 – powerful software for managing, automating and digitizing company processes.
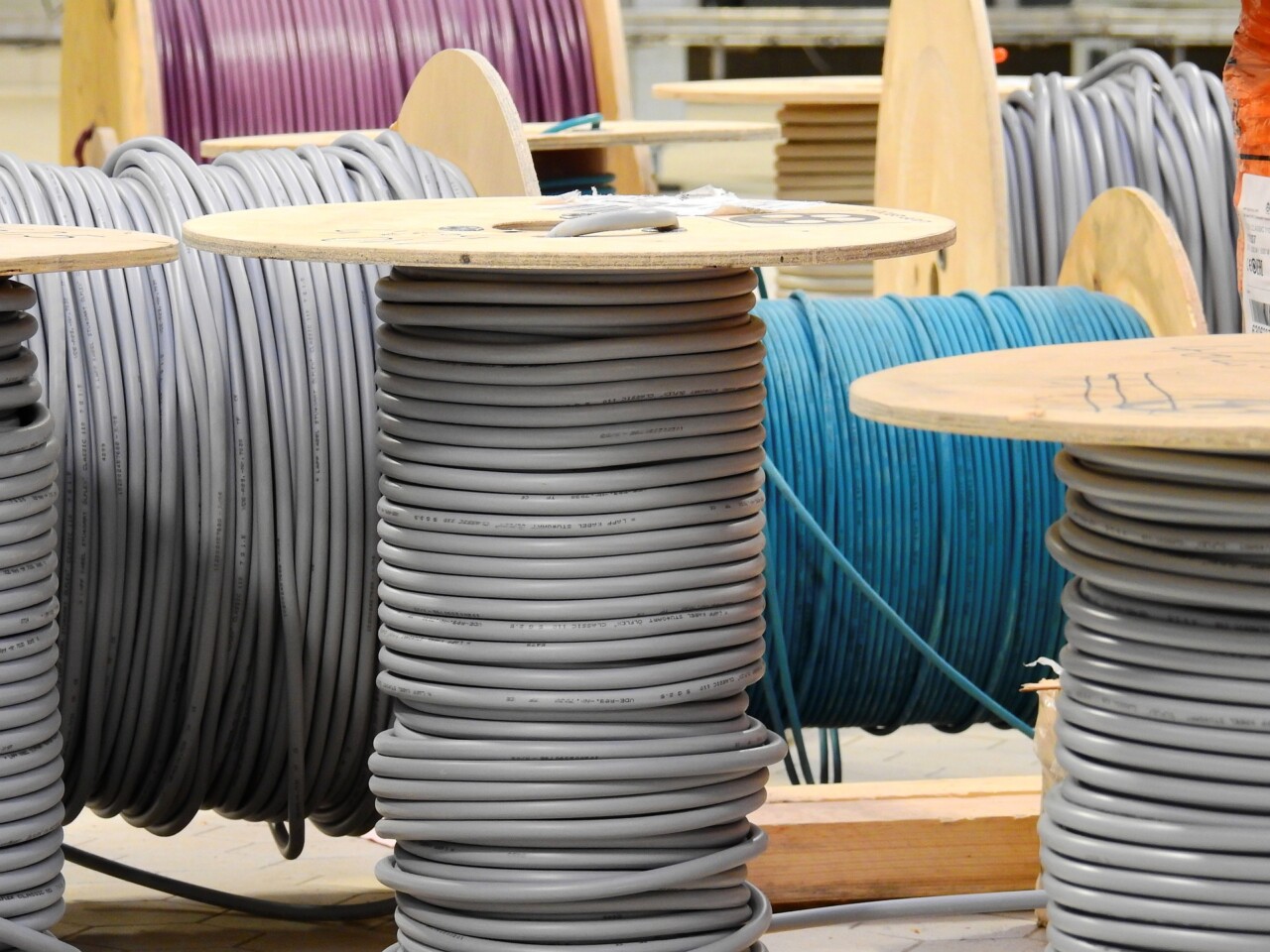
What kind of packaging do we store the goods in?
The method of storage depends on the dimensions and type of goods stored to avoid any damage and ensure the highest safety standards.
For example, we store cable drums on specially designed wooden pallets.
How do we respect the principles of eco-action in our processes?
We use so-called eco-boxes, made from recycled materials. This is one of the elements of our sustainable development strategy, which we are gradually implementing. The benefit to the environment is a benefit to the customer, who, thanks to our eco-activities as a logistics partner, can realize the eco-objectives of his company.
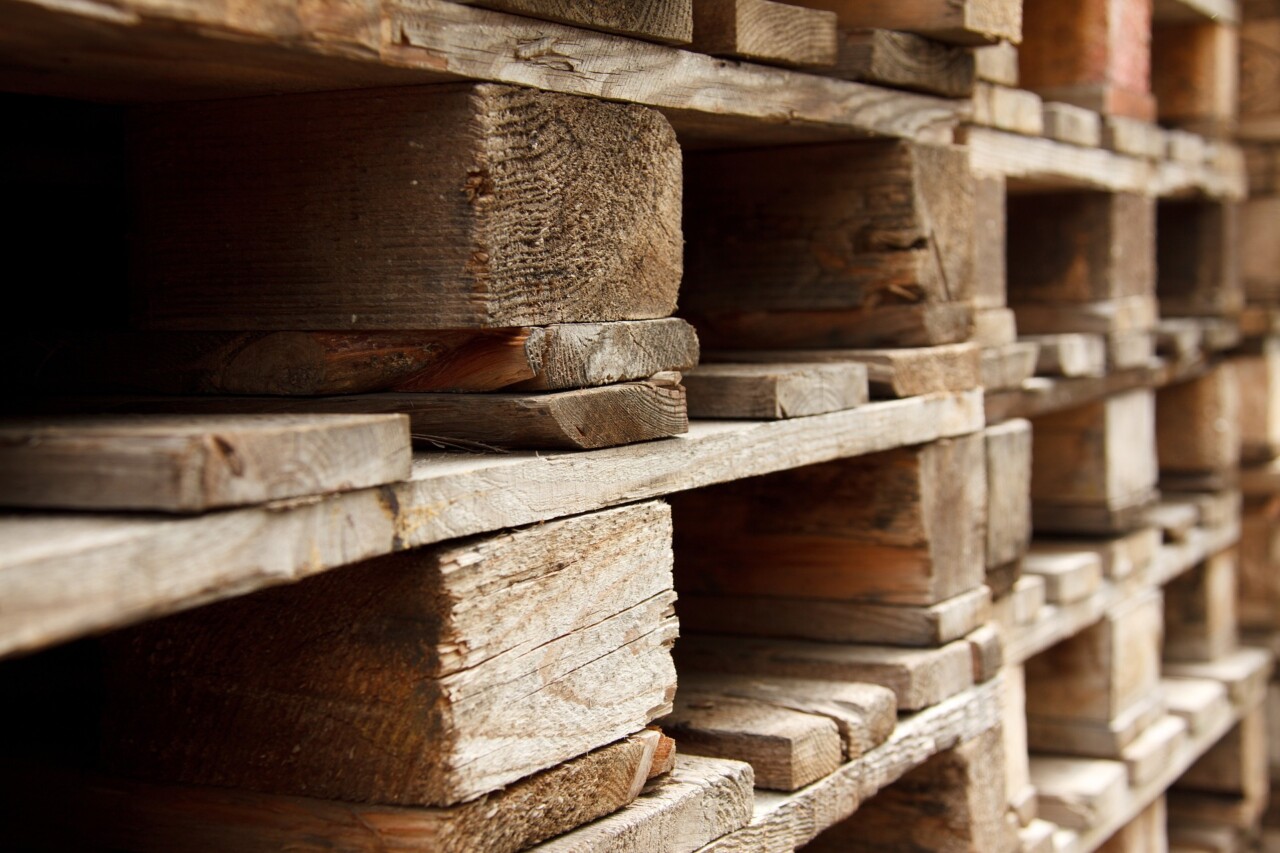
How do we take care of securing the shipped goods?
FCA’s warehouse crew pays special attention when packing shipped goods. Our most important goal is for the product to reach the customer undamaged, and we take care of this when stretching or securing with PP tape.
What is the degree of automation of our processes?
In our facilities, we use a film machine and fill production. All of our equipment undergoes annual inspection, servicing and calibration, so it is always running at top speed. And this guarantees fast customer service time!
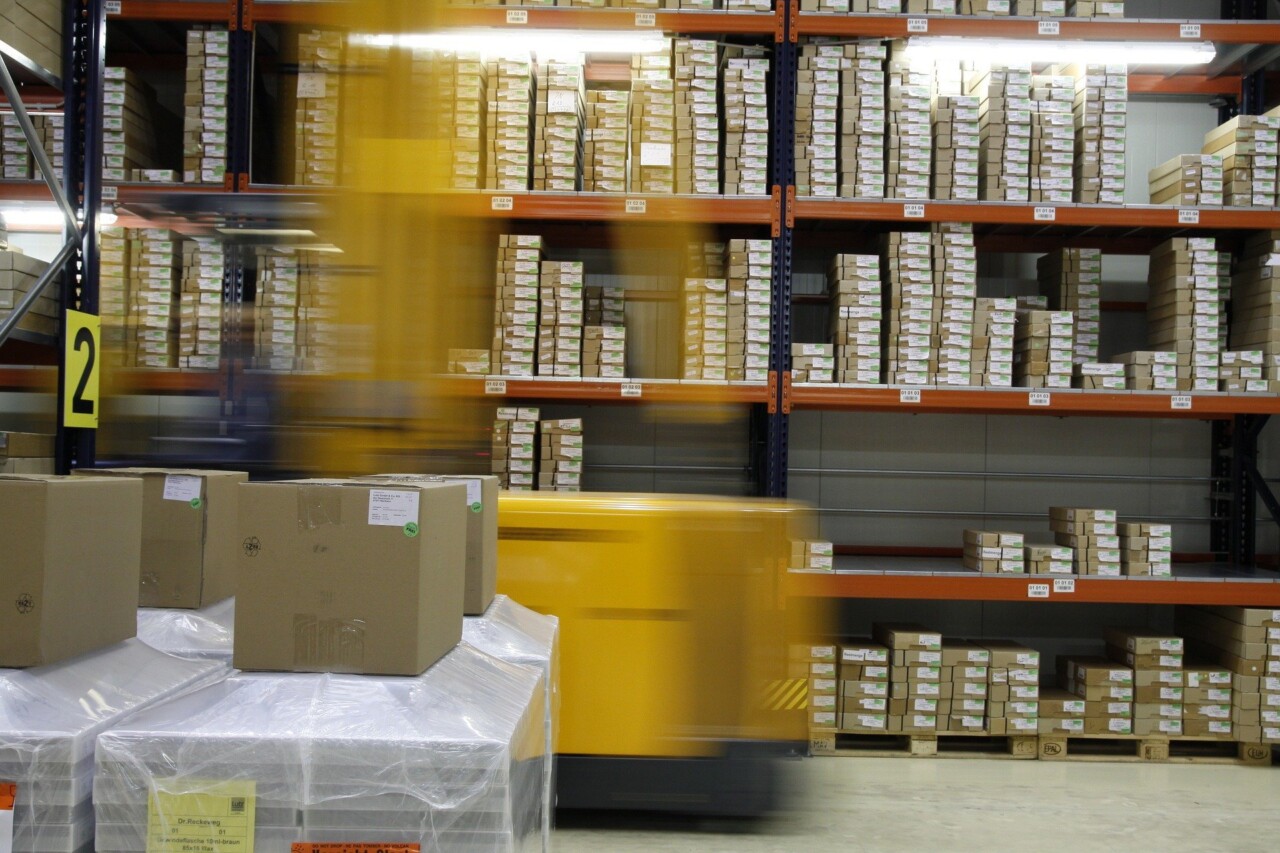
What is the order picking process like?
Orders entered into the WMS system automatically go to fulfillment in the warehouse. Proper ordering and prioritization allows us to have fast order picking time and minimizes the risk of error.
What equipment do we use when working in the warehouse?
What equipment do we use when working in the warehouse?

How long does it take from acceptance to release?
The duration is directly dependent on the complexity of the order. We handle smaller ones on the same business day, and larger ones are ready the day before shipment at the latest – all while maintaining the lead times given to the customer beforehand.
Does the customer have visibility into inventory or shipment history?
All necessary information can be obtained by the customer from the Sales Department, but the customer does not have direct access to it. The salesman, as the customer’s guardian, is happy to answer all questions related to the order and is also available for potential changes due to changing project needs.
Do you have any questions about our storage services?
Get in touch with us!